Considerations for Developing and Testing Inverter-Based Resource (IBR) Models for Grid Interconnection in Hawaii
- ryanquint
- Mar 3
- 4 min read

Author: Goodarz Ghanavati, Principal Engineer, Power System Studies and Modeling, Elevate Energy Consulting
The Hawaiian Electric Company (HECO) has several standards and guidelines for inverter-based resource (IBR) interconnection applicants. These include providing electromagnetic transient (EMT) models — typically built with PSCAD software — that meet certain ride-through and voltage and frequency response specifications. Facilities that use a grid-forming (GFM) inverter must meet additional requirements, including the ability to withstand the loss of the last synchronous machine in the grid and, in some cases, blackstart capability (see Figure 1).
Parties applying for IBR interconnections in Hawaii must understand these requirements to ensure a successful process and avoid costly delays and rework. This post summarizes HECO’s EMT model requirements and how Elevate is supporting interconnection applicants tune models to satisfy the requirements.

Key HECO PSCAD Model Requirements
At a high level, HECO’s requirements cover the following aspects for PSCAD models [1]:
PSCAD Model Submissions: Applicants may submit two PSCAD models—one for normal operation (required) and one with different control settings for black start (optional). If the facility has GFM capability, that should be enabled by default in the model.
IBR Model Quality: All models must meet specific IBR quality and performance requirements [1].
Control Code Implementation: The facility's PSCAD model must implement the actual control code.
Generation Facility Settings: Ride-through and other settings must comply with the power purchase agreement.
Power Plant Controller Configuration: The PPC model should be configured to represent the actual planned implementation.
EMT Model Tuning
In many cases, applicants will have to work with the OEM(s) to tune the inverter and PPC controls in their EMT models to meet HECO requirements. Specifically, GFM inverters must meet more stringent requirements compared to grid following (GFL) inverters and thus are more likely to require some degree of tuning to meet the specific HECO IBR performance requirements and pass the GFM tests.
Figure 2 shows an example of controller tuning in a model for a hybrid solar photovoltaic (PV) plus battery energy storage system (BESS) plant. Initially, the model exhibited undamped oscillations in active power (P) output following a simulation test. Changing the frequency response to a mode with a faster control loop and less filtering significantly reduced the oscillatory response.*
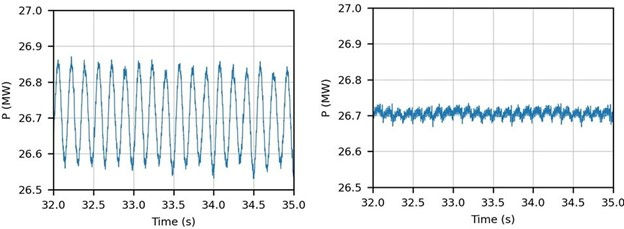
Figure 3 illustrates another example where model tuning was necessary to meet the HECO requirements. In this case, underfrequency protection tripped the inverters during the black start test. Extending frequency protection settings enabled the inverters to initialize properly, pick up the load, and ride through the fault. All these changes, of course, are applied in close consultation with the corresponding original equipment manufacturer (OEM).

Request for Exemption
In some cases, an applicant has a valid technical justification for failing to meet a requirement and can request an exemption from HECO.
For example, Figure 4 shows that the IBR reactive power does not reach steady state within 3 seconds, which is the acceptance criterion for the flat start test [1]. But the OEM confirmed that the model represents the actual startup process for the plant, so accelerating initialization within the model would come at the expense of accurately representing how the plant operates. In this instance, the applicant could potentially request an exemption to HECO’s flat start test requirement by providing its test results along with relevant documentation from the OEM.

Collaboration is Key
While it is often necessary to fine-tune the inverter and PPC settings to comply with the IBR performance requirements, it is imperative that these changes do not inadvertently cause the IBR to fail other tests. Applicants must thoughtfully and preemptively study the updated models to ensure they pass all tests to save time and resources throughout the process. For the best results, applicants should collaborate with other stakeholders including the IBR developer, consultant, and inverter manufacturer(s). Working together will ensure that the site meets the specific needs of the project and complies with the HECO requirements.
Elevate Industry with Expert IBR Interconnection Modeling Support
At Elevate Energy Consulting, we blend our expertise in specialized EMT modeling with strong, effective partnerships with inverter manufacturers and IBR project developers. This synergy enables us to successfully navigate the unique interconnection standards and regulations in Hawaii and other ISO/RTO footprints across North America. Reach out to us at info@elevate.energy to discuss any projects where our team of experts may be able to help with interconnection modeling and studies.
Footnotes:
* Small oscillations remain, but these are common in most practical simulations due to harmonics, negative sequence components, or DC content in waveforms [2].
References:
[1] Hawaiian Electric Generation Facility Technical Model Requirements and Review Process: Transmission or Sus-transmission Interconnected Projects, August 23, 2024.
[2] PSCAD v5.0.2 Application Help.
Comments